In the manufacturing industry, robotic process automation, or RPA, is becoming increasingly popular as a way for businesses to increase efficiency, cut expenses, and improve output. Manufacturers may focus on more strategic operations, increase accuracy, and guarantee better compliance with industry standards by using Robotic Process Automation (RPA) to automate mundane and repetitive work.
Robotic Process Automation (RPA) has a profound impact on the manufacturing industry by fundamentally changing how operations are conducted. It streamlines complex workflows by automating repetitive and time-consuming tasks. This automation minimizes human errors, ensuring consistent product quality and reliable manufacturing processes.
By leveraging RPA, manufacturers can achieve higher productivity, enhanced compliance, and greater flexibility, positioning themselves for sustained growth and competitive advantage in an increasingly automated and data-driven industrial landscape. When taken as a whole, these effects change the manufacturing landscape and promote an atmosphere of innovation, competitive advantage, and constant development.
Benefits of Implementing RPA in Manufacturing
There are several advantages to implementing robotic process automation (RPA) in manufacturing, and these advantages can greatly increase operational efficiency, save costs, and boost overall productivity. Let’s take a look at some of the main benefits:
1. Increased Productivity
- 24/7 Operation: RPA bots may work around the clock without breaks, leading to continuous production and process execution.
- Speed: Because bots are more efficient than people at jobs, they can do tasks like data entry, reporting, and transaction processing much faster.
2. Cost Reduction
- Labour Costs: Automating repetitive and routine processes lowers the demand for manual labour, which results in significant labour cost reductions.
- Efficiency of Operations: RPA lowers overall operating costs by cutting cycle times and simplifying operations.
3. Improved Accuracy and Quality
- Error Reduction: RPA ensures high accuracy and consistency by doing away with human mistakes in tasks like data entry, calculations, and reporting.
- Consistency: Tasks are completed by bots consistently and with a consistent level of quality.
4. Enhanced Customer Experience
- Faster Response Times: Response times can be shortened by automating customer support tasks like order processing and inquiry handling.
- Accuracy: Ensuring timely updates and correct order fulfilment increases client trust and happiness.
5. Scalability
- Flexibility: Without the need for extra human resources, RPA solutions can be readily scaled up or down to handle different job volumes.
- Adaptability: RPA is easily modified to meet new criteria and processes as business demands change.
What are the key processes to automate in the Manufacturing sector
Robotic process automation (RPA) improves the manufacturing sector by automating repetitive activities. For example, to provide the best possible inventory management, bots coordinate data changes between systems, keep an eye on stock levels, and automatically place new orders for supplies.
By examining capacity and demand projections, they optimize production schedules and work in tandem with QC systems to uphold product standards. Robotic Process Automation (RPA) greatly increases manufacturing productivity and operational effectiveness by decreasing manual labor, minimizing errors, and increasing efficiency.
Let’s now discuss some key process that can be automated by manufacturing businesses:
1. Production line automation
Automation of the production line refers to using technology to complete activities on the manufacturing line with the least amount of human intervention.This approach enhances efficiency, accuracy, and productivity in manufacturing processes. The salient features are as follows:
- Robotic Integration
- Automated Conveyance Systems
- Quality Control Mechanisms
- Data Analytics and Monitoring
- Integration with IoT
- Scalability and Modularity
Implementation Steps
1. Choosing the Right Technology:
- Choose the right PLCs, software, conveyors, and robots.
- Verify that it works with the current systems.
2. System Integration:
- Integrate new automated systems into the ongoing activities.
- Incorporate IoT and data connectivity.
3. Validation and Testing:
- Test systems thoroughly to make sure they function properly.
- Verify performance and quality criteria.
2. Inventory management
The activity of supervising and managing the movement of products into and out of a company's inventory is called inventory management. To guarantee adequate supply availability while lowering carrying costs, it entails keeping an eye on inventory levels, tracking stock movements, and optimising inventory turnover. Important components of inventory control consist of:
- Inventory Tracking
- Demand Forecasting
- Order Management
- Inventory Optimization
- Supplier Relationship Management
- Warehouse Management
- Inventory Valuation
- Inventory Analysis and Reporting
Implementation Steps
- Identify Tasks for Automation:
- Determine repetitive inventory management tasks suitable for RPA, such as data entry, stock monitoring, and order processing.
- Data Transmission and Setup:
- Move current inventory information to the new inventory management system from spreadsheets or outdated systems.
- To guarantee correctness and integrity, cleanse and validate the data.
- Integration with Existing Systems:
- Connect the inventory management system to accounting software, point of sale (POS), enterprise resource planning (ERP), and other corporate apps and systems.
- Go-Live and Deployment:
- Establish an official go-live date for the inventory management system's complete deployment.
- During the early deployment stage, keep an eye on user adoption and system performance.
- Continuous Monitoring and Optimization:
- Review and audit inventory data, procedures, and system utilisation on a regular basis.
3. Supply chain optimization
The goal of supply chain optimisation is to maximise efficacy and efficiency at every stage of the supply chain, from locating raw materials to shipping completed goods to clients.The key features of supply chain optimization include:
- Demand Forecasting and Planning
- Inventory Optimization
- Supplier Relationship Management
- Transportation and Logistics Optimization
- Risk Management and Resilience
- Performance Measurement and Continuous Improvement
Implementation Steps
- Tool Selection & Integration:
- Choose the appropriate RPA software that aligns with your supply chain needs and integrates seamlessly with existing systems.
- Integrate RPA bots with supply chain management systems, ERPs, and other relevant software to facilitate data exchange and task automation.
- Pilot Testing & Full Deployment:
- Implement RPA bots on a small scale to test functionality and performance. Monitor bot behavior, gather feedback, and make necessary adjustments.
- Roll out RPA solutions across the entire supply chain process, ensuring proper training for users and stakeholders.
- Optimising Inventory Management:
- Use inventory optimisation strategies including demand-driven replenishment, safety stock optimisation, and just-in-time (JIT) inventory.
- For real-time inventory tracking, monitoring, and replenishment, make use of inventory management tools and technologies.
- Continuous Improvement and Performance Measurement:
- To assess progress towards goals and monitor supply chain performance, use metrics and key performance indicators (KPIs).
- To find areas for improvement and promote ongoing optimisation efforts, do post-mortem evaluations, root cause analyses, and frequent performance reviews.
How Nected can help in RPA for Manufacturing Industry
Efficiency and adaptability are critical for success in the manufacturing industry's ever-changing landscape. Robotic Process Automation (RPA) presents itself as a game-changing technology that enables manufacturers to boost efficiency, spur innovation, and automate monotonous operations.
Now we’ll see how a top workflow automation platform such as Nected can use RPA to transform manufacturing operations. We'll show how Nected expedites business growth, optimises resource utilisation, and streamlines procedures using inventory management as an example.
Step 1: Defining tasks that can be automated
First we need to decide what tasks need to be automated. For instance, following tasks in inventory management can be automated:
- Automated inventory monitoring and replenishment - RPA can continuously monitor inventory levels and take necessary actions when they fall below reorder point
- Automated notification for inventory depletion - RPA can alert stakeholders when necessary conditions are satisfied via SMS, emails, integrated messaging services etc.
- Automated purchase order generation - RPA generates purchase orders automatically when inventory levels are low and purchase orders can be filled with product details and quantities sent to suppliers.
Taking example of checking if the inventory levels fall below the reorder point and purchasing the products through Supplier’s API endpoint, we can perform it by setting up the triggers.
Step 2 : Setting up API triggers
1. Trigger setup: Set up an API trigger to start the process when particular parameters are satisfied. Establish the trigger that will go off when the inventory level is lower than the reorder point.
2. Goal: The trigger acts as a spark to automate the process of replenishing supplies. When inventory levels need to be replenished, the process will automatically generate purchase orders by setting up the trigger
Log into your Nected account and go to the workflow creation portal to get started. To begin setting up the workflow for automatic inventory management, click the "Create Workflow" option.
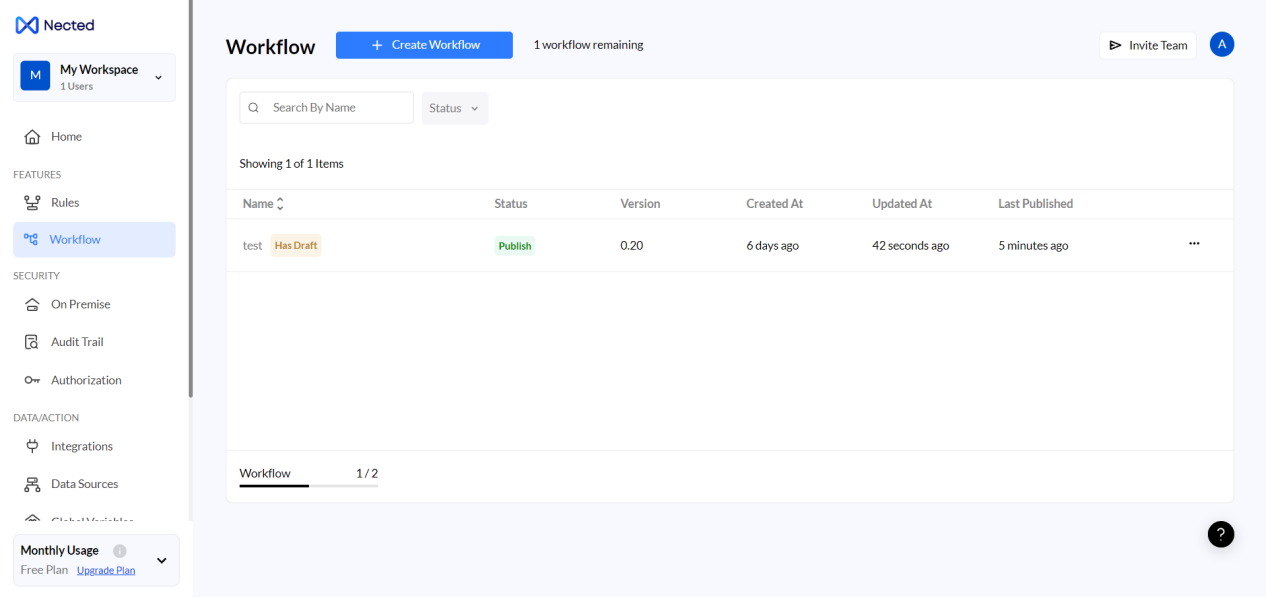
After creating a new workflow, create the API trigger to start the with the workflow process
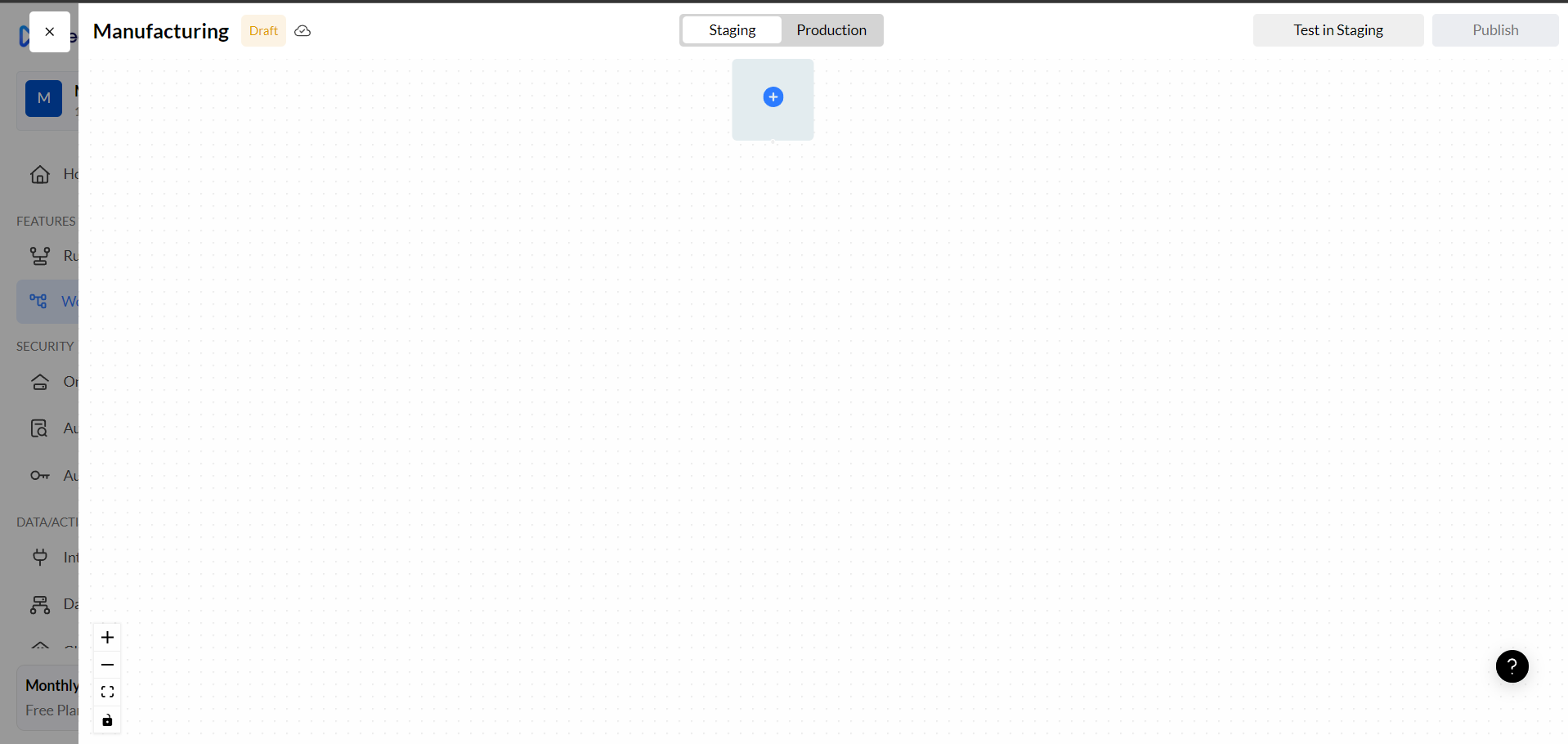
Step 3 : Setting up input parameters
- inventory_level: Represents the current stock level of a particular inventory item.
- reorder_point: Specifies the threshold at which inventory levels trigger the need for replenishment.
- supplier_api_endpoint: Identifies the API endpoint used to communicate with the supplier for inventory replenishment.
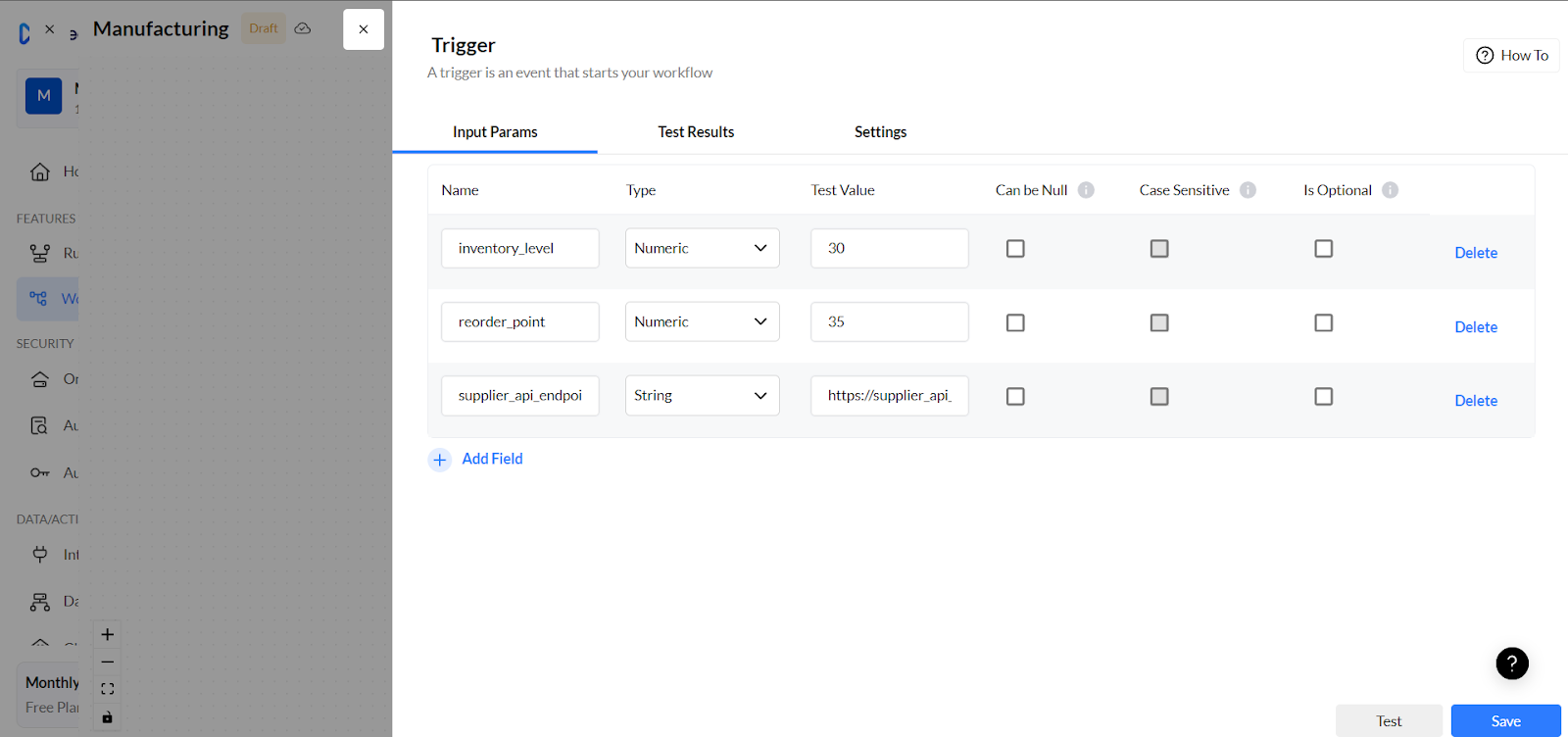
Step 4 : Defining actions and conditionsActions in the workflow are based on the results of the conditions evaluated:
- Rule configuration :
Rule name : reorder_point_check Condition : Checks if inventory levels are below reorder point
- Actions based on rule outcome :
If true : Triggers a REST API node which is used to send a POST request to the supplier for inventory replenishment If false : Do nothing
Here in the automation we can add a new “rule” node :
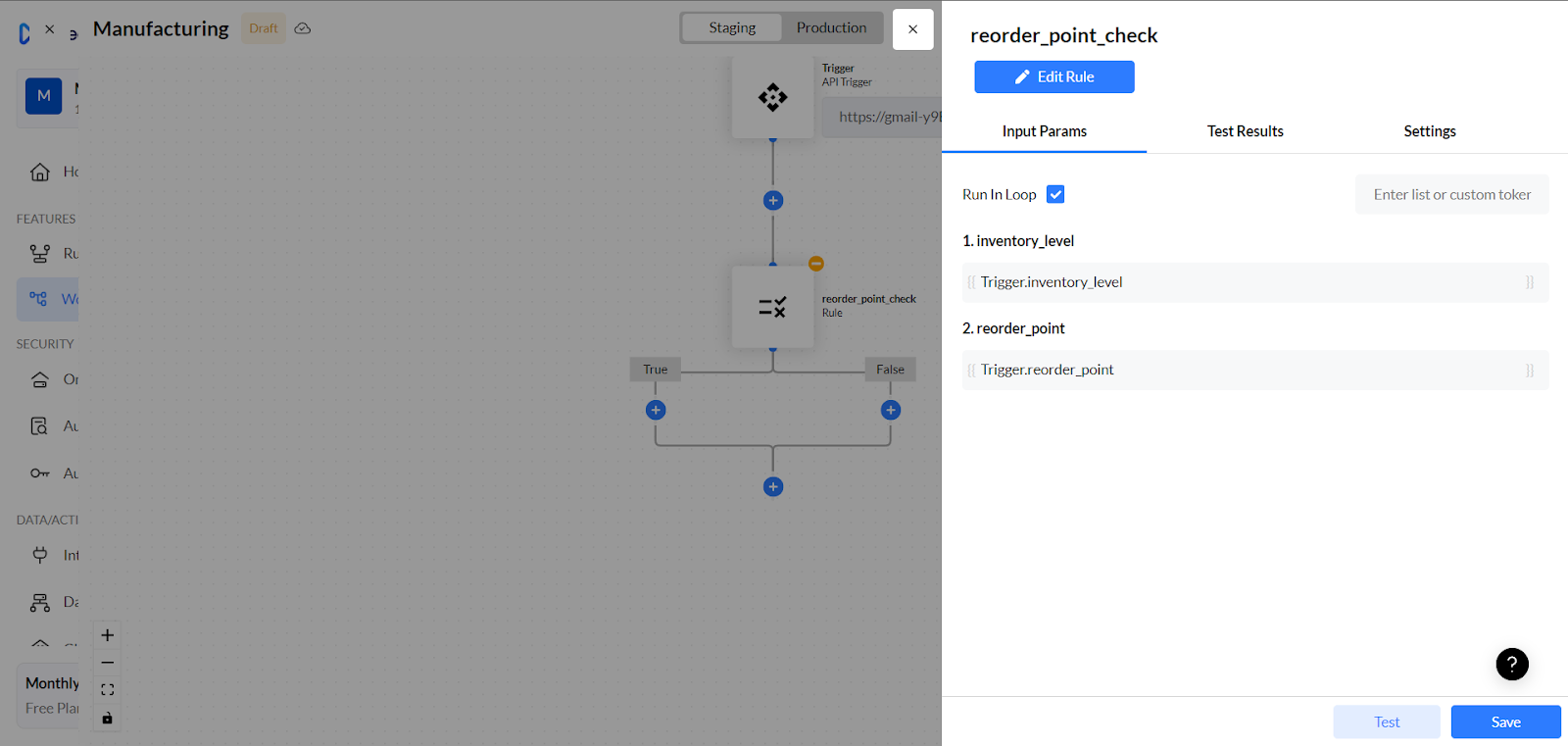
This node triggers our rule “reorder_point_check” :
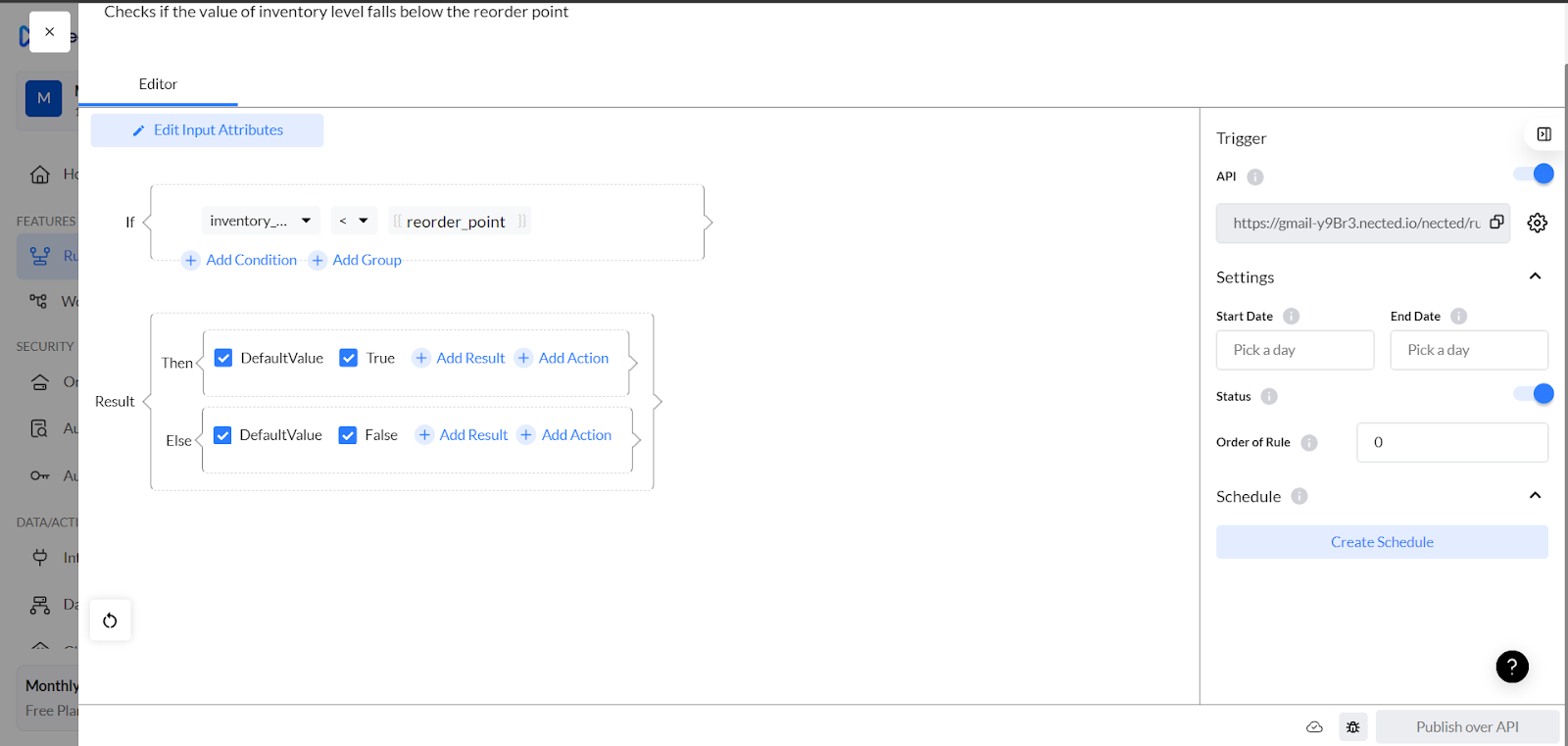
Flexibility in Actions
The Nected platform allows for a great deal of freedom when designing actions depending on the results of workflows:
1. Restocking Triggered: Automatically start the restocking process when inventory levels drop below the reorder point.Adapt the process so that it can automatically update inventory records, send purchase orders, and connect with suppliers.2. Successful Replenishment: Upon successful processing of replenishment requests, take the necessary steps to update inventory records and verify the delivery of supplies.
Depending on what we need, we can add nodes to our workflow.
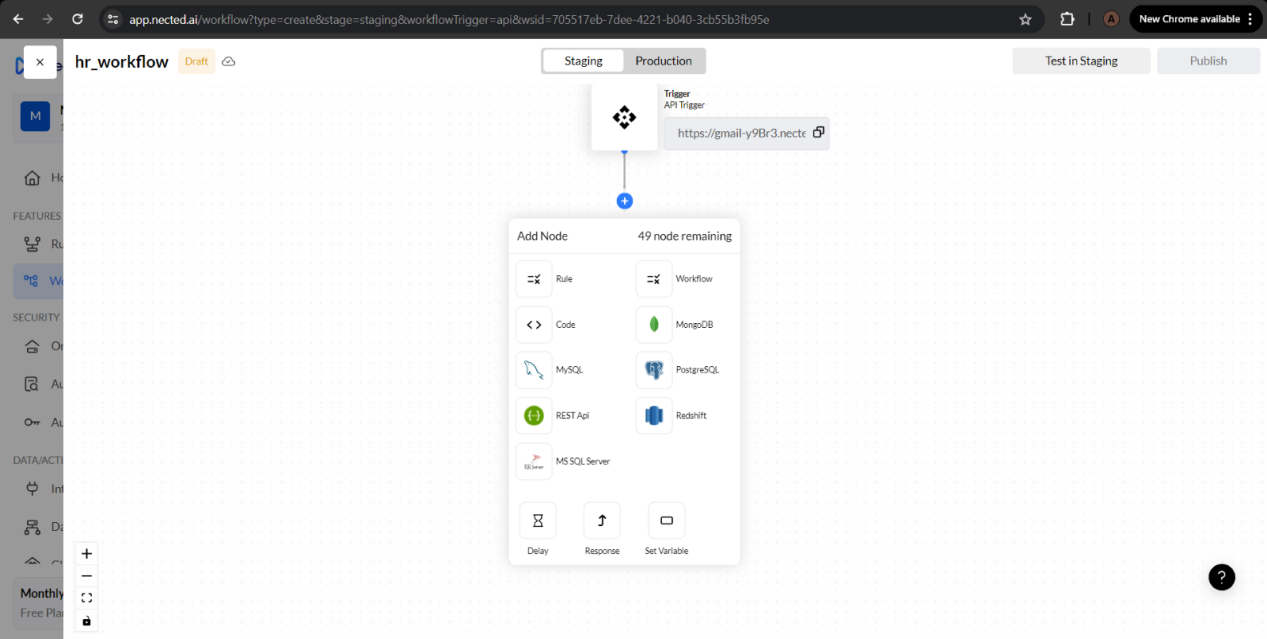
(You can take these nodes: Rule , Workflow, Code , Database Connector such as MongoDB, MySQL, PostgreSQL, Redshift , Rest API)
For our current example, we will add our Rest API node “supplier” from Integrations in Nected :
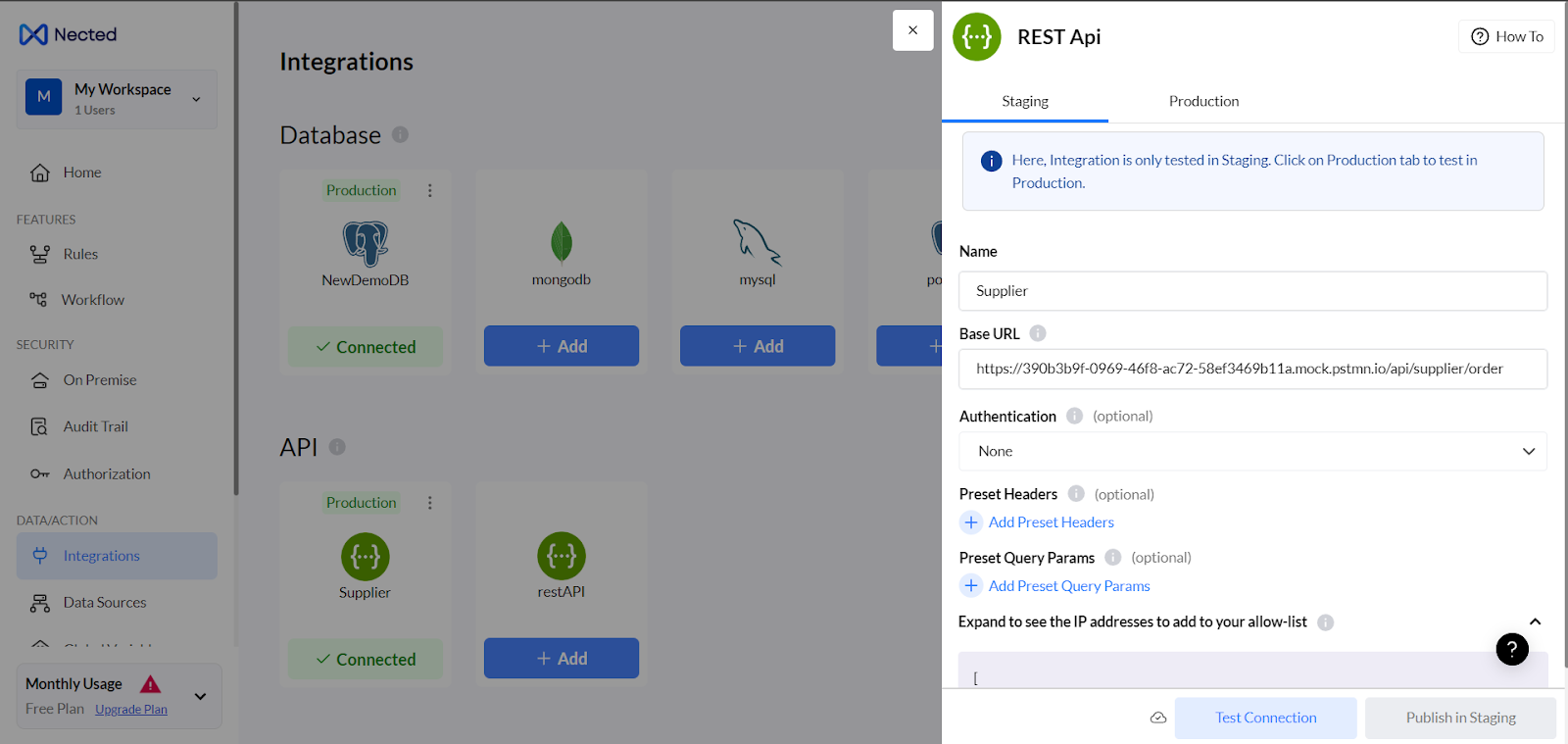
We can configure the node according to our use cases :
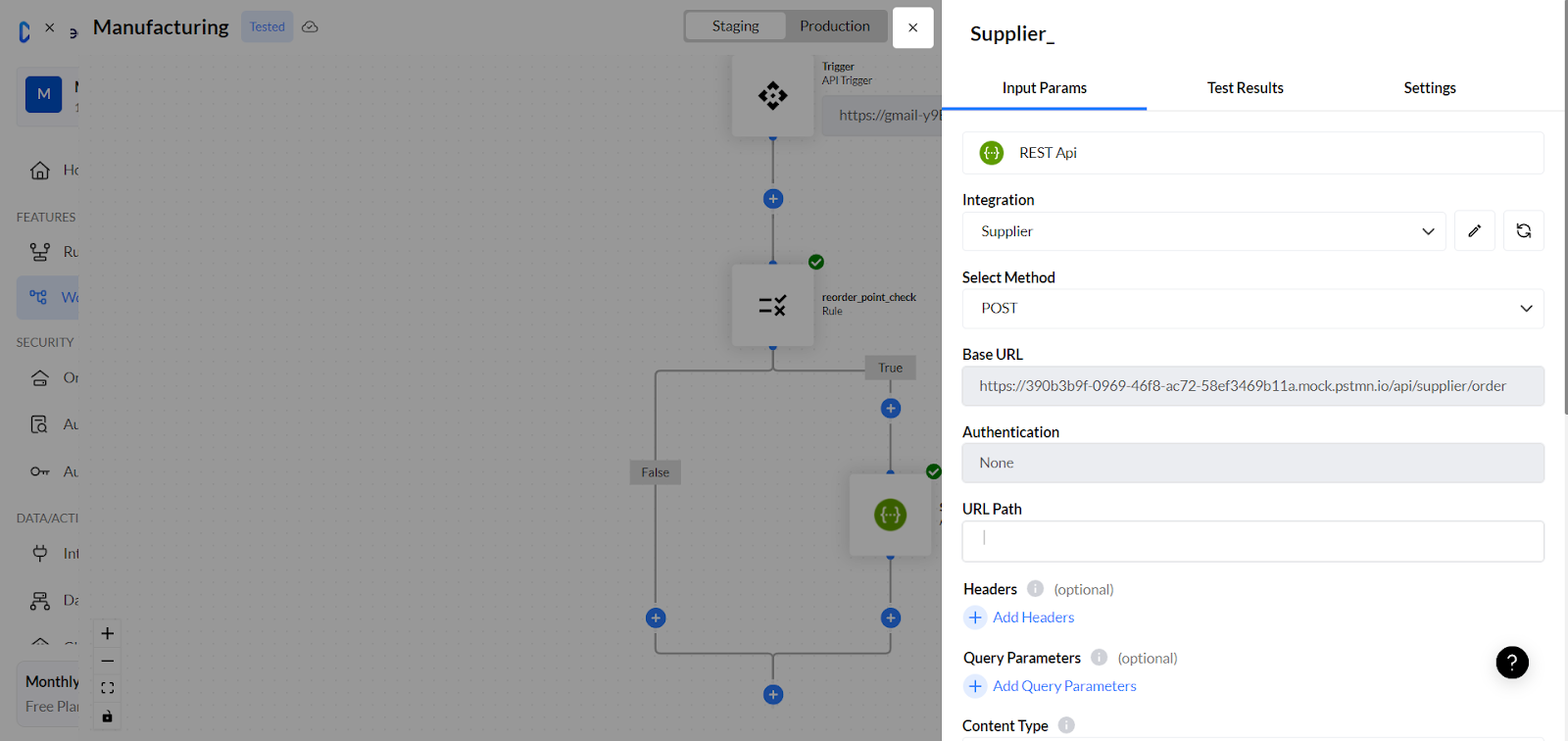
After completion of the workflow, you can test and publish it.
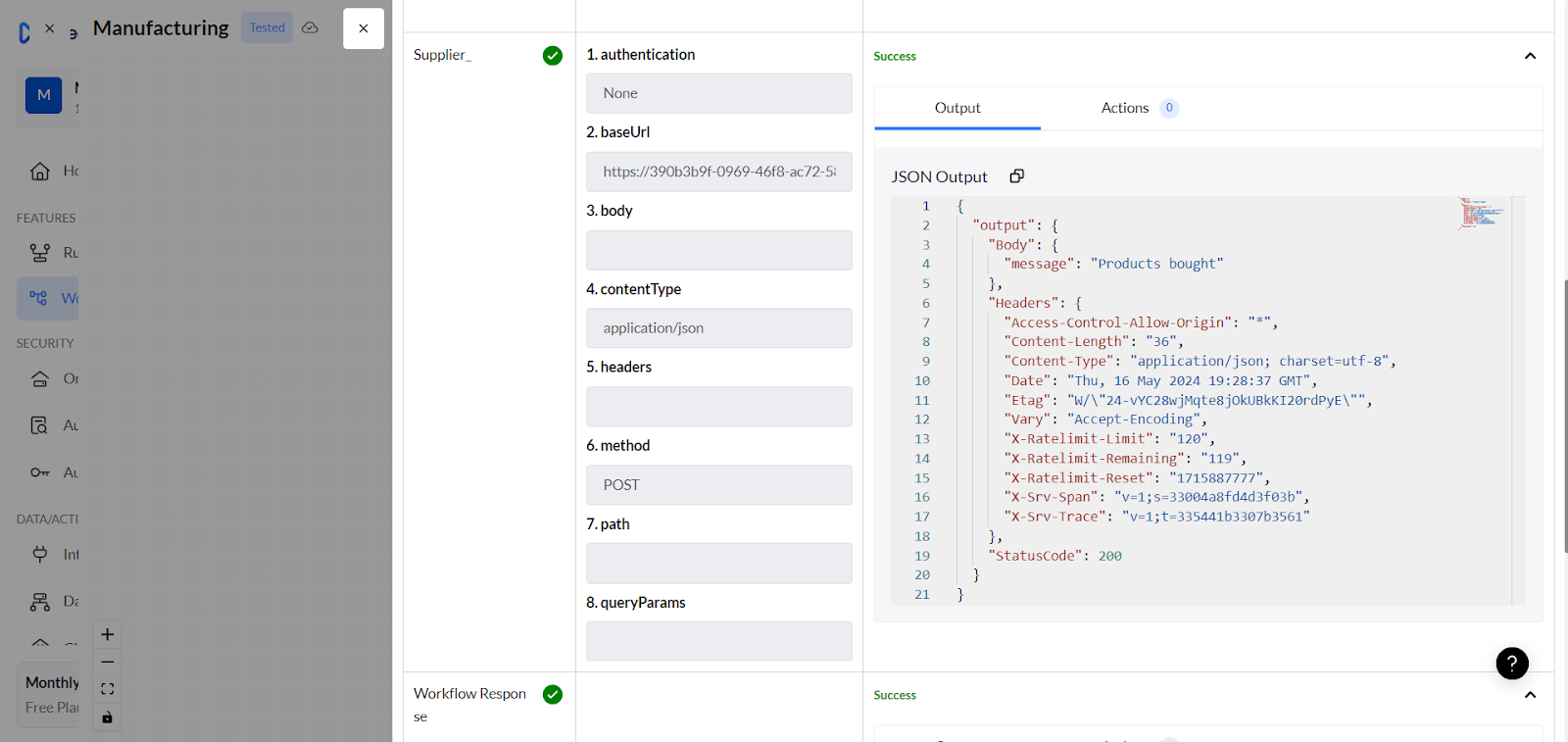
Explore the power of RPA with Nected and revolutionize your manufacturing processes today.
Conclusion
To put it concisely, manufacturing has been transformed by robotic process automation (RPA) fostering innovation, and automates repetitive labour. When combined with cutting-edge technologies like AI and IoT, RPA improves optimisation and decision-making. It ensures adaptability to changing market needs by fostering agility, flexibility, and collaborative workflows.
RPA promises to improve further as it develops, setting up manufacturing for long-term growth and competitiveness in the contemporary environment.
FAQs
Q1. How does RPA impact the workforce in manufacturing?
By relieving workers of menial, repetitive duties, RPA can help manufacturing organisations restructure their workforce by enabling them to concentrate on higher-value, more strategic activities like innovation, problem-solving, and customer interaction.
Q2. What distinguishes RPA in production from conventional industrial robots?
RPA uses software robots that mimic human behaviours to automate digital operations, as opposed to traditional industrial robots, which are physical machines built to carry out specific tasks. In general, RPA is more adaptable, simpler to set up, and compatible with current IT infrastructure without requiring major changes.
Q3. What are some successful use cases of RPA in manufacturing?
Automation of order-to-cash procedures, invoice processing, inventory reconciliation, quality assurance inspections, production scheduling, and compliance reporting are just a few of the manufacturing applications of RPA that have proven successful.
Q4. What developments in RPA for manufacturing can we anticipate?
Future developments in RPA in manufacturing could involve the following: a greater focus on scalability, flexibility, and agility in manufacturing operations; a greater adoption of cognitive automation and AI integration; an expansion of RPA into fields like predictive analytics and predictive maintenance; and further development of collaborative robots, or cobots.