The use of robotic process automation (RPA) in logistics transforms the industry by streamlining operations, reducing errors, and improving efficiency. Logistics operations often face numerous challenges, including high operational costs, manual errors, and complex supply chain management.
Implementing RPA can address these issues by automating repetitive tasks, improving accuracy, and providing real-time data insights. The logistics industry is quickly changing with new technologies like Artificial Intelligence (AI), Internet of Things (IoT), and Robotic Process Automation (RPA).
These trends include using AI to make better decisions and forecasts, IoT for real-time shipment tracking, and robots in warehouses for picking, packing, and managing inventory. Additionally, RPA helps automate customer service, providing quick responses and real-time updates.
This blog will provide a comprehensive overview of how RPA is transforming logistics, delving into specific use cases such as order processing, inventory management, shipment tracking, and customer service automation. Additionally, we'll discuss the benefits of RPA, implementation strategies, and real-world success stories.
By the end of this blog, you will have a clear understanding of the transformative power of RPA in logistics and how it can drive efficiency and growth in their operations.
What is Robotic Process Automation in Logistics Systems?
Robotic process automation in logistics systems refers to the use of software robots or "bots" to automate repetitive, rule-based tasks within the logistics and supply chain management processes.
These bots mimic human interactions with digital systems to perform various functions such as data entry, order processing, shipment tracking, and customer service operations.
For example, in order processing, RPA tool can handle tasks such as receiving orders, verifying them, and generating invoices automatically. This streamlines the process and reduces errors.
Similarly, in inventory management, an RPA solution can monitor inventory levels, send restocking alerts, and generate detailed reports, ensuring smooth warehouse operations and optimal stock levels.
What Are the Key Areas of RPA Application in Logistics?
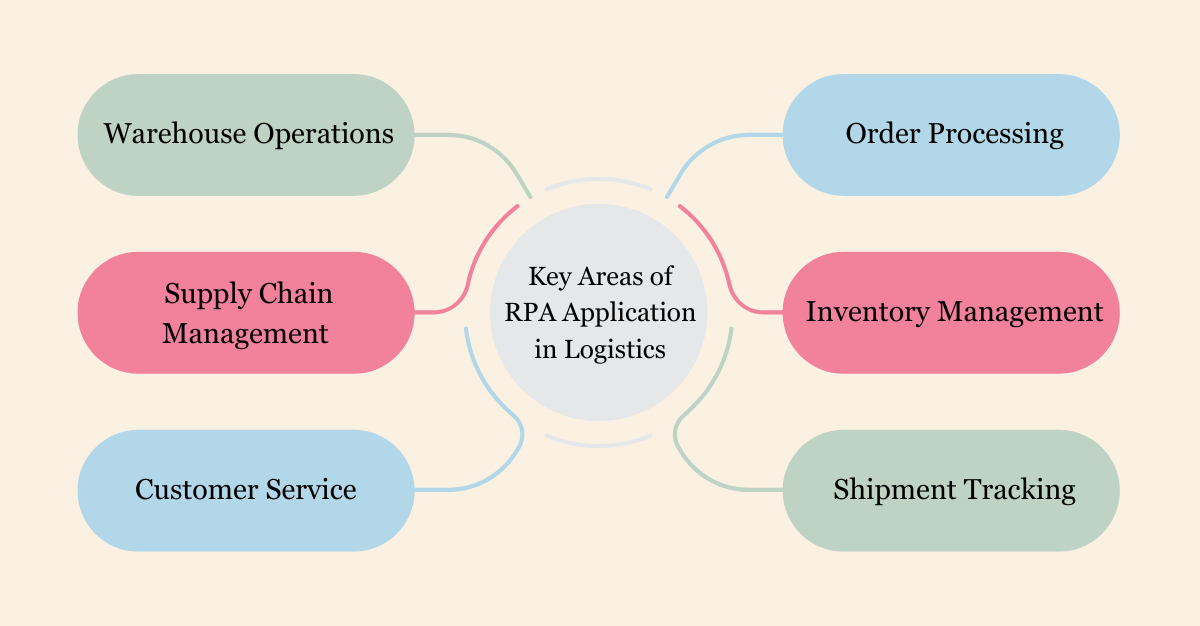
1. Order Processing: RPA streamlines order processing by automating tasks such as order receipt, verification, and updating of order statuses. This reduces manual errors and accelerates order fulfillment, ultimately enhancing customer satisfaction through faster processing times.
2. Inventory Management: In logistics, RPA provides real-time inventory tracking and restocking alerts, optimizing inventory levels and preventing stockouts or overstock situations. Additionally, it generates detailed inventory reports for informed decision-making by management.
3. Shipment Tracking: RPA automates real-time shipment status updates and customer notifications, improving transparency and trust by keeping customers informed throughout the delivery process. Moreover, it efficiently manages exceptions such as delays or lost shipments.
4. Customer Service: Through RPA, logistics companies can handle routine customer inquiries, process returns/refunds, and speed up response times, thereby enhancing customer satisfaction. This automation also frees up customer service agents for more complex tasks, improving overall service quality.
5. Supply Chain Management: RPA automates procurement processes, supplier tracking, and purchase orders, forecasting demand and adjusting supply chain activities accordingly. It enhances visibility into the supply chain for proactive issue resolution, ensuring smooth operations.
6. Warehouse Operations: RPA automates picking, packing, and inventory updates in warehouse operations, coordinating seamlessly with automated storage systems. By increasing productivity and reducing errors, RPA optimizes warehouse processes, leading to greater efficiency.
Let’s take a process example to automate using an RPA solution.
In this scenario, we will automate the order processing and management workflow using Nected to streamline operations, reduce manual errors, and improve efficiency. The automation will cover tasks such as receiving orders, verifying details, updating inventory, and notifying customers.
Step-by-Step Implementation
Step 1. Initial Setup in Nected
First, you have to access your Nected account and log in with your credentials.
Then, you have to create a new workflow. To do this, navigate to the Workflow section and select "Create New Workflow."
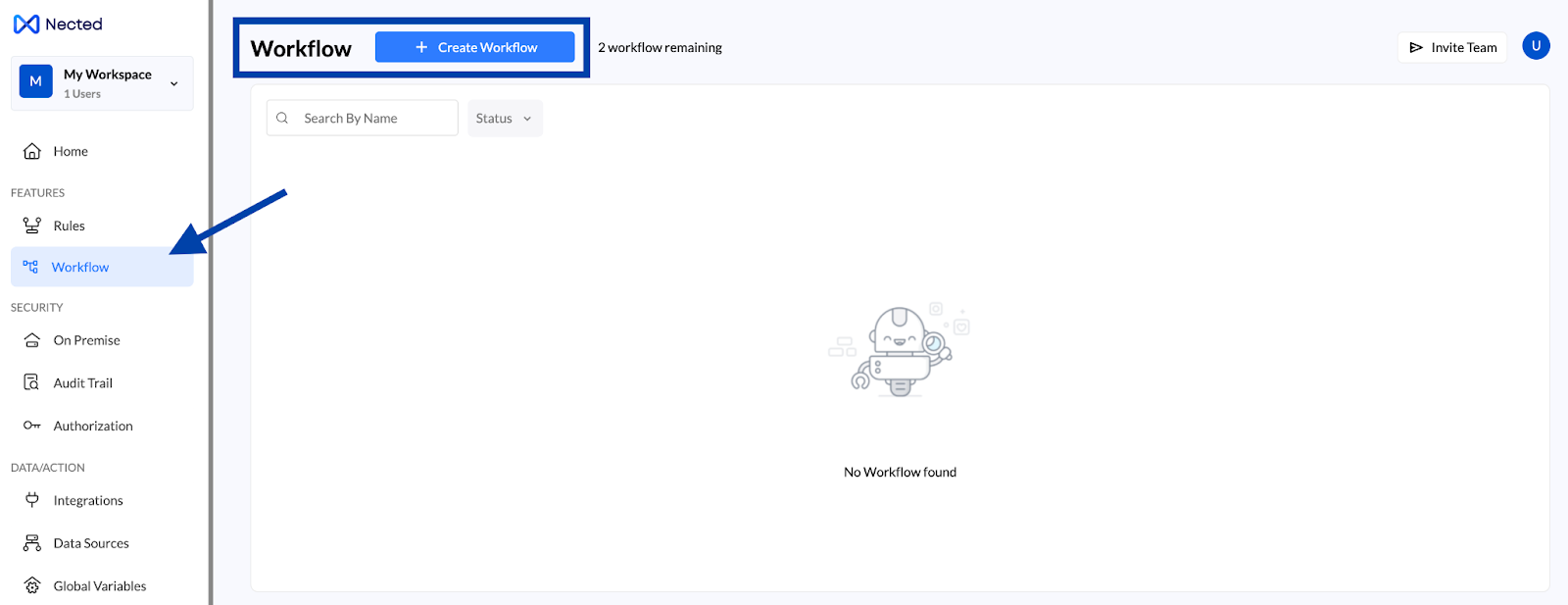
Step 2. Define the Workflow
Name and Describe the Workflow.
In this example, we have given the name: "Automated Order Processing”
And, set the description as: "Automates the order processing tasks including order receipt, verification, inventory update, and customer notification."
Select the Trigger: Choose the trigger that will initiate the workflow, such as receiving an order email or a new entry in the order management system.
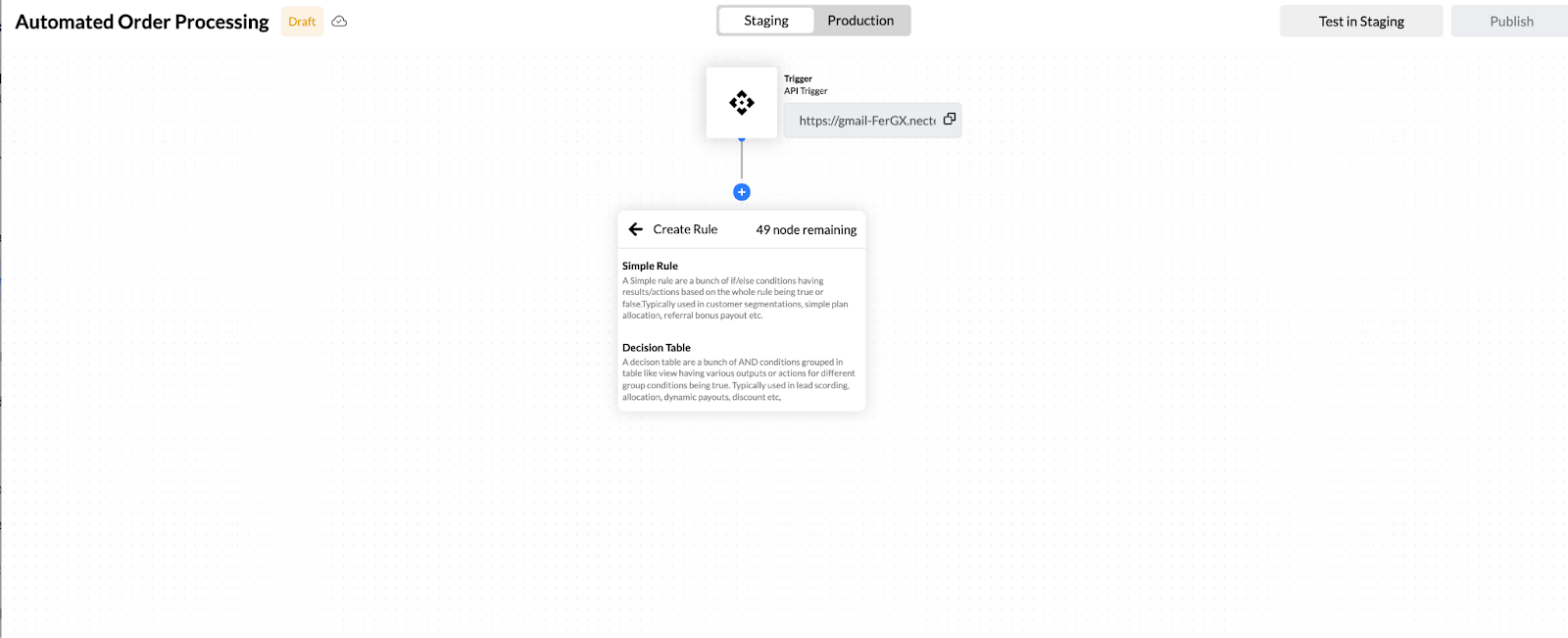
Step 3. Configure Input Variables
Now, you have to create input variables.
- Customer ID
- Order ID
- Product ID
- Order Quantity
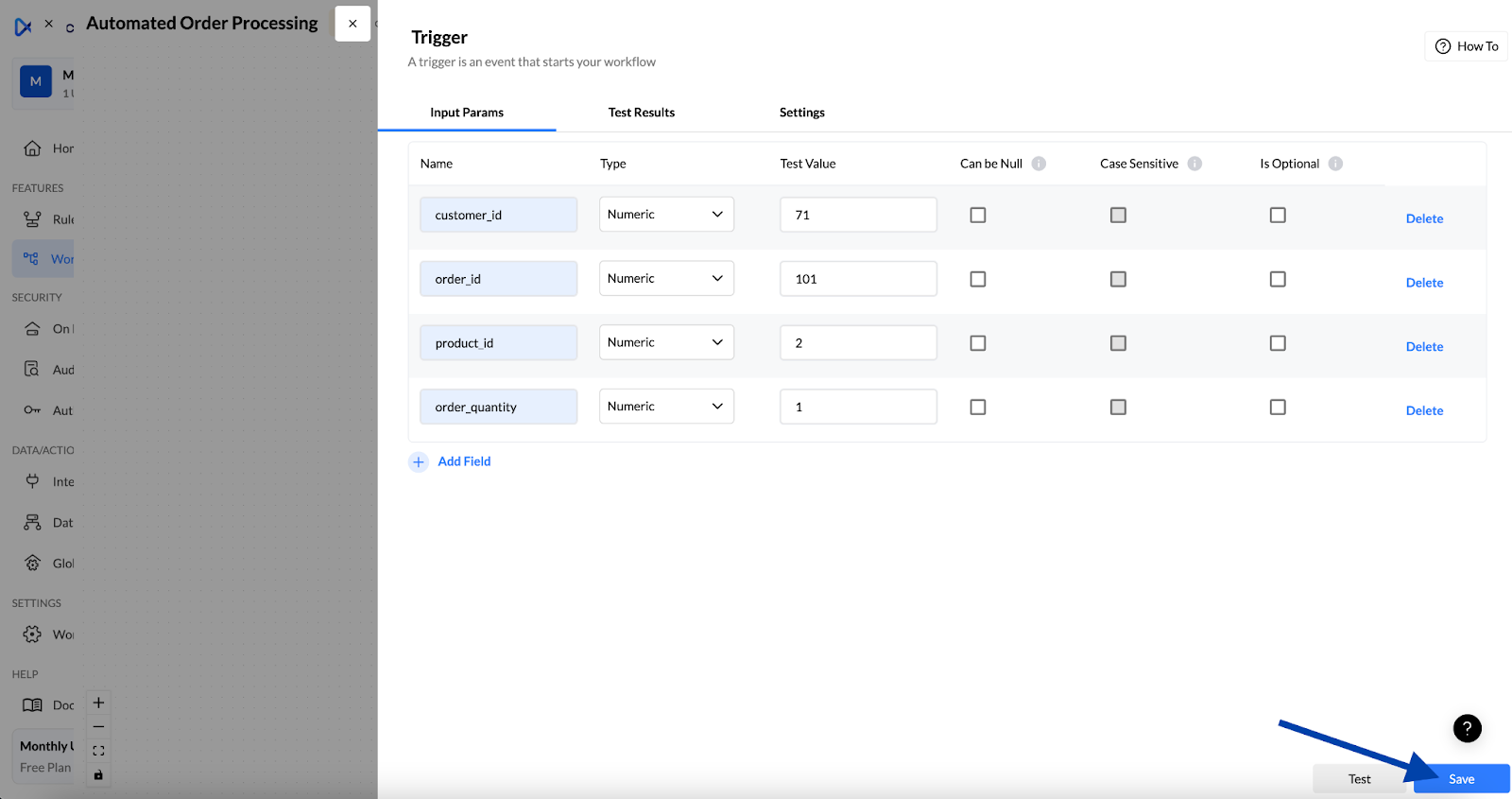
Step 4. Automate Order Receipt and Verification by adding actions and rules
Following the API trigger setup, actions or rules are added to define what the workflow will execute. For example, actions could include sending a confirmation email to the customer, updating the order details, or notifying about product relevant staff.
Nected allows for the integration of custom rules and JavaScript codes, enhancing the workflow's capabilities and ensuring all steps are executed as intended.
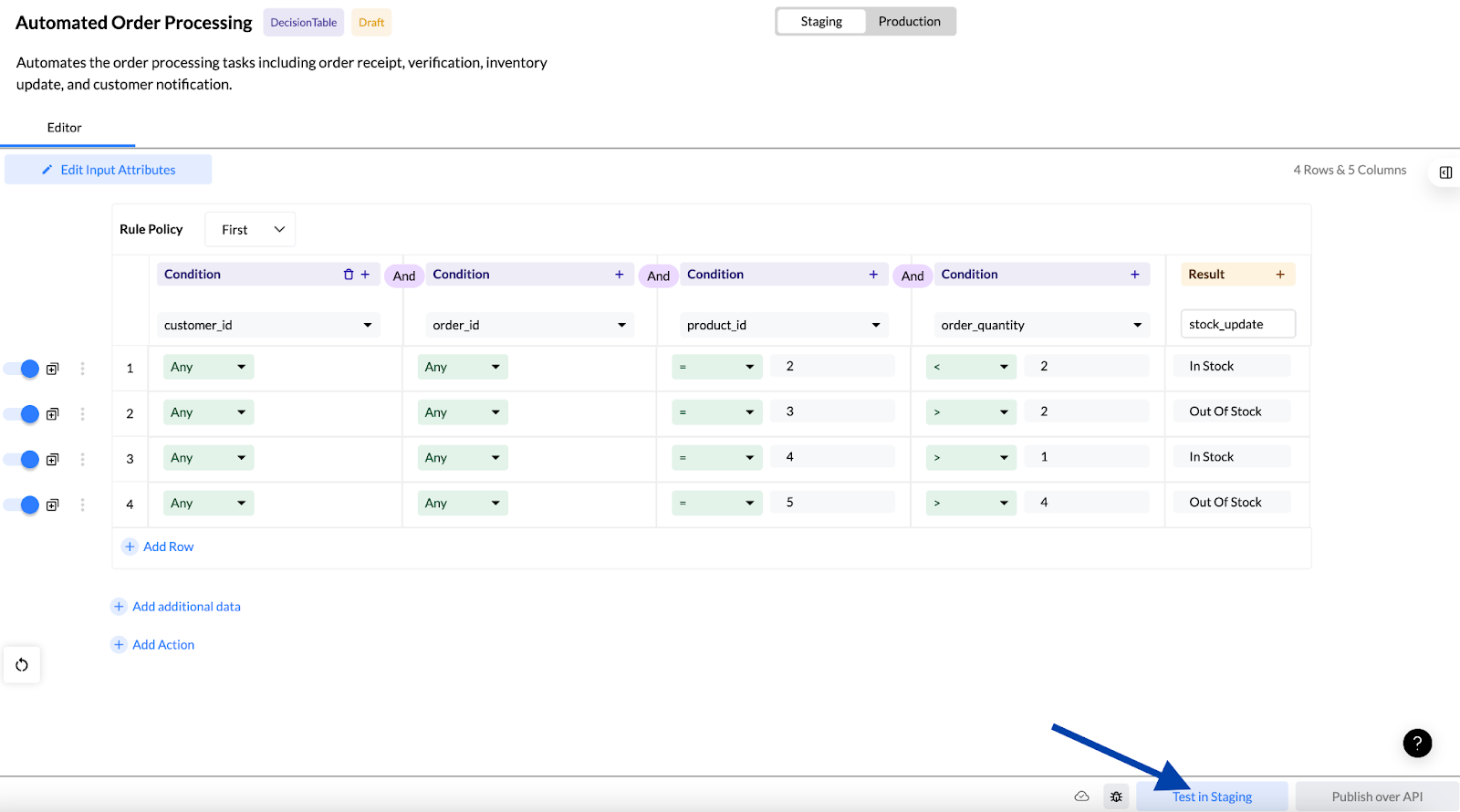
Step 5: Testing each node
Before deployment, thoroughly test every aspect of the workflow, including the API trigger, all actions, and rules.
- For instance, you can configure the workflow to check the current inventory levels for ordered products. If stock is low, trigger an alert or an automated restocking request.
- Automate sending an order confirmation email or SMS to the customer, including details like order ID, products ordered, and expected delivery date.
- Once the order is shipped, automatically send the customer a tracking link.
Comprehensive testing ensures the workflow performs seamlessly and reliably once live.
Run the workflow in a staging environment to ensure all steps are functioning correctly.
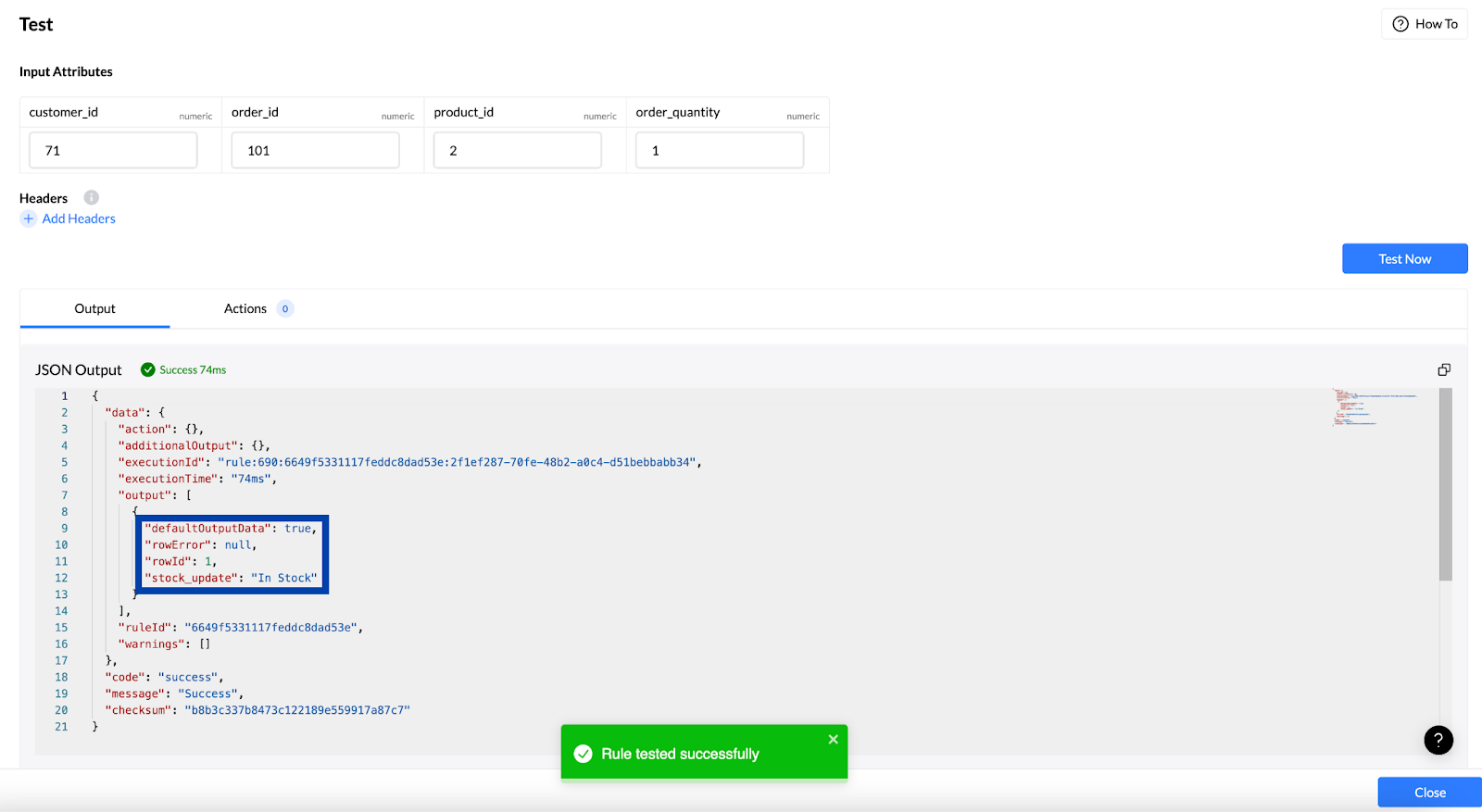
Validate that orders are processed accurately and notifications are sent promptly. Once testing is successful, deploy the workflow to the live environment.
Step 6: Publishing workflow
After successful testing confirms the workflow functions correctly, you can publish it. Nected ensures a workflow can only be activated if all its components, including rules, are in a published state. Clicking the ‘Publish’ button activates the workflow, automating the designated process and enhancing overall efficiency and patient experience.
For a detailed step-by-step guide on creating workflows using Nected, check out this video:
Key Benefits of RPA in Logistics
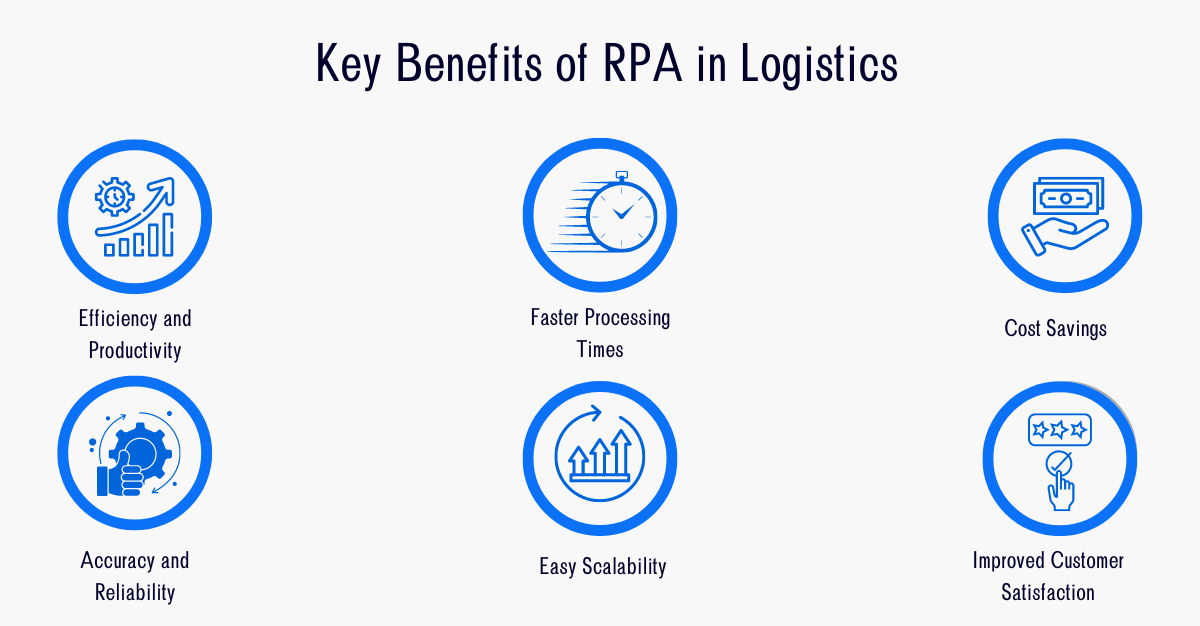
Utilizing RPA in logistics, you can gain the following benefits:
1. Efficiency and Productivity: RPA streamlines logistics operations, automating repetitive tasks and freeing up employees to focus on more strategic activities. This boosts overall efficiency and productivity across the supply chain.
2. Faster Processing Times: By automating tasks like order processing and inventory management, RPA reduces processing times significantly, ensuring timely delivery of goods and services to customers.
3. Cost Savings: RPA helps reduce operational costs by minimizing manual labor, eliminating errors, and optimizing resource utilization. This leads to significant cost savings for logistics companies.
4. Accuracy and Reliability: Automation through RPA ensures accuracy and reliability in data processing and decision-making, reducing the risk of errors and improving the quality of service provided to customers.
5. Easy Scalability: RPA allows logistics companies to scale their operations up or down based on demand fluctuations easily. Bots can handle increased volumes of transactions without the need for additional human resources, ensuring flexibility and agility.
6. Improved Customer Satisfaction: With faster processing times, accurate order fulfillment, and timely updates, RPA enhances the overall customer experience. This leads to higher customer satisfaction and loyalty, contributing to the long-term success of logistics businesses.
Check out 5 Best Open Source workflow automation software.
Why Choose Nected For Robotic Process Automation in logistics?
Nected is a no-code/low-code workflow automation platform. It offers a comprehensive solution for RPA in logistics to streamline operations and overcome common challenges in the industry.
Capabilities of Nected:
User-Friendly Interface: Nected features an intuitive user interface that allows users to design, deploy, and manage RPA workflows with ease, without the need for extensive coding knowledge.
Advanced Automation Tools: With Nected, businesses can automate a wide range of tasks in logistics operations, including order processing, inventory management, shipment tracking, and customer service, among others.
Scalability: Nected's platform is designed to scale seamlessly based on business needs, allowing companies to adapt to changing demands and handle increased volumes of transactions efficiently.
Integration Capabilities: Nected can integrate with existing logistics systems and software, enabling smooth data exchange and collaboration across different platforms.
Real-Time Monitoring and Reporting: Nected provides real-time monitoring and reporting features, allowing businesses to track the performance of RPA workflows and identify areas for optimization.
Check how Nected helps overcome challenges in logistics:
Efficiency and Productivity: By automating repetitive tasks, Nected enhances efficiency and productivity in logistics operations, reducing manual errors and accelerating processing times.
Cost Savings: Nected helps businesses save costs by minimizing labor expenses, optimizing resource utilization, and reducing operational inefficiencies.
Accuracy and Reliability: With Nected's advanced automation tools, businesses can ensure accuracy and reliability in data processing and decision-making, leading to improved service quality and customer satisfaction.
Customer Satisfaction: By automating customer service processes, Nected enables businesses to provide faster responses, accurate information, and personalized support to customers, enhancing overall satisfaction and loyalty.
Flexibility and Adaptability: Nected's scalable platform allows businesses to scale their RPA initiatives according to changing demands and market dynamics, ensuring long-term success and competitiveness in the logistics industry.
Conclusion
The implementation of RPA in logistics offers numerous benefits that can significantly enhance operational efficiency and improve customer satisfaction.
By automating repetitive tasks such as order processing, inventory management, and shipment tracking, logistics companies can streamline their operations, reduce errors, and accelerate processing times.
The accuracy, reliability, and scalability provided by RPA ensure that logistics operations can adapt to changing demands and maintain a competitive edge in the industry. The value of using robotic process automation in logistics cannot be overstated.
Not only does it optimize processes and drive cost savings, but it also enables logistics companies to deliver faster, more accurate, and more reliable services to their customers. By leveraging RPA technology, businesses can unlock new levels of efficiency and productivity, paving the way for sustainable growth and success in today's dynamic marketplace.
Choose Nected to build the advanced systems needed to transform your logistics operations and stay ahead of the competition.
FAQs
Q1: How can RPA streamline order processing and management in the logistics industry?
RPA streamlines order processing and management in logistics by automating tasks such as order receipt, verification, updating order statuses, and generating invoices. This reduces manual errors, accelerates order fulfillment, and enhances customer satisfaction through faster processing times.
Q2: Can RPA be integrated with existing logistics systems and software?
Yes, RPA can be integrated with existing logistics systems and software to automate tasks and processes seamlessly. It can work alongside existing ERP (Enterprise Resource Planning) systems, WMS (Warehouse Management Systems), TMS (Transportation Management Systems), and other logistics software.
Q3: What are the potential cost savings associated with implementing RPA in logistics?
The potential cost savings associated with implementing RPA in logistics include reduced labor costs, minimized errors and rework, optimized resource utilization, and improved operational efficiency.
Q4: How does RPA impact customer service in the logistics industry?
RPA impacts customer service in the logistics industry by automating responses to customer inquiries, processing returns/refunds, and providing real-time order and shipment status updates. This speeds up response times, enhances customer satisfaction, and frees up customer service agents for more complex tasks.
Q5: What are some real-world examples of successful RPA implementations in logistics?
Real-world examples of successful RPA implementations in logistics include automating order processing and inventory management for eCommerce retailers, optimizing route planning and delivery scheduling for transportation companies, and streamlining customs clearance processes for freight forwarding companies.